Striving towards Industry 5.0 – What does the future factory look like?
Author: Teemu Turunen
Estimated reading time: 9 minutes
Many associate industrial activities with smokestacks, water pollution, and reports of factories closing due to unprofitability. In reality, industrial operations are currently undergoing a significant transformation. Digitalization is playing an increasingly prominent role in manufacturing, and clean production technologies are becoming mainstream. Innovation, especially in the fields of bioeconomy and circular economy, is thriving as raw materials and materials are utilized across industry boundaries.
Industrial activities play a vital role in the fight against climate change both now and in the future: 45% of greenhouse gas emissions in the EU-27 area1 and 20% of all emissions come from industrial activities. Furthermore, only 12% of the raw materials used by industry are recycled2. The Green Deal recognizes the role of industry, and the EU has formulated a vision of Industry 5.0 to achieve a technological leap toward more sustainable production operations. This new vision builds upon the previously discussed Industry 4.0 concept, adding depth and comprehensiveness3.
What could Industry 5.0 mean in practice? What might the future factory look like? Let’s explore the possibilities in the 2030s from different perspectives.
Industry 4.0
- Centred around enhanced efficiency through digital connectivity and artificial intelligence
- Technology – centred around the emergence of cyber-physical objectives
- Aligned with optimisation of business models within existing capital market dynamics and economic models – i.e. ultimately directed at minimisation of costs and maximisation of profit for shareholders
- No focus on design and performance dimensions essential for systemic transformation and decoupling of resource and material use from negative environmental, climate and social impacts
Industry 5.0
- Ensures a framework for industry that combines competitiveness and sustainability, allowing industry to realise its potential as one of the pillars of transformation
- Emphasises impact of alternative modes of (technology) governance for sustainability and resilience
- Empowers workers through the use of digital devices, endorsing a human-centric approach to technology
- Builds transition pathways towards environmentally sustainable uses of technology Expands the remit of corporation’s responsibility to their whole value chains
- Introduces indicators that show, for each industrial ecosystem, the progress achieved on the path to well-being, resilience and overall sustainability
Starting with customer and stakeholder needs
Sara is about to go hiking in Norway and needs a new hiking jacket. She found a suitable one online and is now picking it up from a self-service kiosk. The jacket’s features have been customized for her from dozens of product variations, a common practice in production.
The jacket’s digital product passport has recorded production conditions, allowing Sara to trace the origins of the raw materials all the way back to their source. This ensures that the stated sustainability criteria have been met throughout the jacket’s life cycle. In fact, the product passport contains a vast amount of information that different stakeholders can access according to their needs.
Instead of a single entity handling all production stages, production now occurs in industrial production ecosystems where each player specializes in their area.
Unlike before when Sara’s jacket might have been manufactured in China, this product didn’t travel far. The clothing brand decided to invest in a new production facility in Finland, where ESG (Environmental, Social, Governance) matters are taken seriously. Factors influencing the location decision included Finland’s stable industrial policy, long traditions in refining, easy availability of skilled labor, and nearby logistics chains for raw materials.
- Products are becoming increasingly customized.
- Logistics chains are transparent.
- Factory location depends on multiple factors, not just production costs.
Innovative production ecosystems
Several players are involved in making Sara’s hiking jacket. The first has produced the raw material for hemp yarn, which Sara selected as the fabric base. The next player has started producing the yarn, utilizing not only hemp but also various other ecological raw materials such as wood, straw, recycled plastic, and glass wool. The clothing brand’s production unit further refines the yarn, manufacturing the jacket and adding the specified features.
Sara chose a coating for her jacket that naturally repels mosquitoes. The active substance is derived from basil and patented by a biotech company, which supplies it for various applications. Additionally, the jacket features printable sensor technology to measure moisture and temperature on the inner surface, automatically opening small ventilation channels created during the manufacturing process.
Instead of a single entity handling all production stages, production now occurs in industrial production ecosystems where each player specializes in their area. This allows for better customization of products and faster market entry for innovations. These players are located on the same industrial campus, forming innovative development environments. Their required data is collected in a shared cloud, managing the supply chain and distributing data to each player as needed. Individual players no longer need to worry about factory assets; they are purchased as services from specialized providers.
- Specialized players collaborate within new production ecosystems.
- Traceability and digital product passports ensure transparency in production.
- Shared infrastructure enhances efficiency.
Sustainability as an integral part of production
A service provider manages the factory’s energy and utility production, owning the infrastructure and selling the utilities to each player as a service. This particular factory primarily uses electricity generated from clean wind power. Due to fluctuating electricity prices, a synthetic methane gas boiler is used when necessary.
Resilience is built into energy production, with key components duplicated, and storage capacity available for both electricity and heat. Energy recycling is maximized within the factory, and heat pumps produce temperatures exceeding 180°C for curing the coating.
Water usage has been minimized, although the factory is not yet completely closed-loop. However, wastewater from the process is utilized, serving as dilution water in another company’s processes. The factory only releases sanitary water, which is captured and used for city district heating through a low-temperature district heating network.
Efficiency is still emphasized, but the term used is no longer “energy efficiency” but rather “efficiency indicator,” calculated by artificial intelligence. It considers various efficiency aspects, including energy, raw materials, energy prices, and order volume. It is noteworthy that recycled raw material fractions are increasingly used, making raw materials more heterogeneous. However, automation, advanced sensor technology, and artificial intelligence enable stable and adaptable production processes. Improved control algorithms also mean that overproduction is no longer necessary.
- Energy and utilities are procured as services.
- The main energy source is electricity, but alternatives are available.
- Systems are designed for resilience and flexibility.
- Water use efficiency is increasingly important.
- Production capabilities enable using lower-quality and more heterogeneous raw materials.
Changing roles for employees
Working in manufacturing has changed significantly since the 2020s. In the control room for the fabric production process sits Pekka, who spent his earlier career in a plywood factory. He can apply his previous manufacturing expertise in this role but has also had to learn many new skills.
In Pekka’s current position, the most important tasks involve validating control changes proposed by artificial intelligence and monitoring quality – not all aspects of quality assurance can be done mechanically. AI doesn’t autonomously control processes but suggests changes, with final decisions made by humans. Fortunately, these systems are user-friendly, and Pekka has learned to use them easily by utilizing the factory’s digital twin. It also assists in other training sessions, and the project department uses it for planning and simulation of new investments.
Analyzer data is also updated into digital twin models. Realistic data is continuously available for training, real-time optimization, and project management needs.
The most significant change in Pekka’s work has come from robots, which handle physical tasks. His previous duties were physically demanding, leading to musculoskeletal problems. In fact, it is not even possible to walk near the operating machines anymore; they are enclosed for safety. This change is reflected in safety statistics: the last significant accident occurred 1,789 days ago. Overall, working conditions have improved significantly, with robotic cleaners maintaining the cleanliness of production facilities. Real-time IoT sensors monitor and adjust air quality throughout the production hall.
Meaningful work for Pekka comes from mentoring. The mentor-apprentice model has returned, with both sides learning from each other. The new generation has a lot to offer in terms of improving factory operations. Pekka’s mentee handles both production tasks and maintenance duties since versatility is now favored.
- Manual labor is decreasing, with robots used in new applications.
- AI and digital twin applications are widely used in production.
- Versatility and continuous learning are valued.
- Workplace environments are maintained as healthy and safe.
- Usability is a key aspect of system design.
Digitalization as the backbone of production
As mentioned earlier, production operators receive support from various intelligent applications in their daily work. However, utilizing these applications requires a vast amount of data. Data is collected traditionally into a centralized automation system but is increasingly refined and analyzed in the cloud. In addition, Internet of Things (IoT) devices collect extensive data outside the core process, which is integrated into the same database as process data.
Data is also obtained from supply chains, allowing for seamless traceability back to the origins of raw materials. It is noteworthy that the same measurement data is used extensively for different purposes, flowing seamlessly between different systems and interfaces.
For example, a sophisticated particle analyzer has been incorporated into the hemp pulp manufacturing process. It analyzes both the composition of the pulp and impurities within it. Composition data primarily helps in process control, but when processed, it is also made available on various data-driven dashboards, enabling the factory’s engineering team to leverage AI-processed information. Similarly, impurity particle data is crucial for maintenance, allowing for the prediction of potential equipment breakdowns and the maintenance of spare parts inventory.
Analyzer data is also updated into digital twin models. Realistic data is continuously available for training, real-time optimization, and project management needs.
- Data is increasingly used throughout the entire value chain and life cycle.
- IoT application utilization is expanding, but not all data goes to the cloud.
- Predictive maintenance models become more precise, and their applications expand.
- The digital twin is actively used for various needs.
Emphasis on anticipation and flexibility
Today, maintenance operations look like this: Sini, who works in the maintenance department, retrieves the 3D model of a coating spray nozzle from the library and sends it to a 3D printer for production. While waiting for the nozzle to be completed, Sini assists the project department. They are currently reconfiguring the layout of one factory section to introduce fire-resistant coating for construction industry applications. The layout change is straightforward because the utility connections and foundations were designed to be flexible and adaptable from the beginning.
At the end of the day, Sini reviews the predictive maintenance application. She notices that an automatic order has been placed for a pump impeller, which has a 92% likelihood of being needed within the next month.
- 3D printing is an integral part of maintenance.
- The layout can be easily modified.
- Inventory management and maintenance are based on continuous anticipation.
Necessary conditions for success are already in place
Elements like those described above are already in use in various industries, and similar applications will become more widespread in the future – a comprehensive industrial transformation is just beginning. Particularly intriguing pioneers are new technology startups building their production operations “from scratch” and reshaping the prevailing production landscape. This should be a lesson for all of us: it is crucial to develop new opportunities from the early stages of facility planning.
Watch the video on Elomatic’s approach to the digitalization of factories
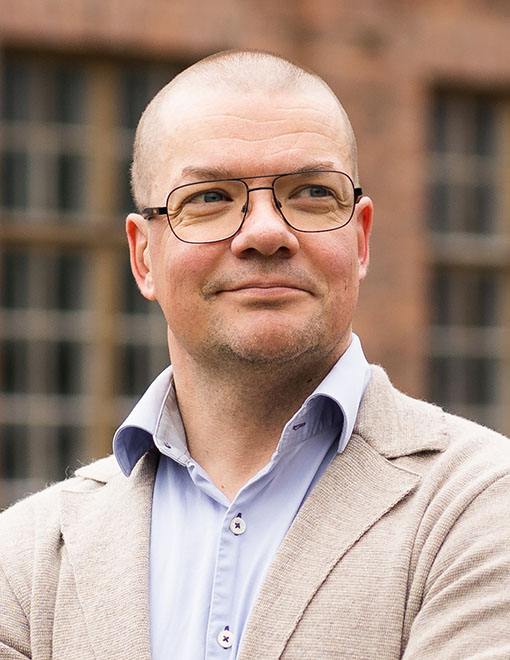
Teemu Turunen
Phil. Lic.
(Env. Science)
Teemu has extensive experience in energy and process consulting in several industries. He currently works as Business Development Director in the energy and process business area. His focus is to lead the development of sustainable solutions for future needs.
teemu.turunen@elomatic.com
Want to know more? Check out these related articles:
Smart Factory investment and production development
We offer solutions and support for individual production development needs – regardless of whether your issue concerns a machine, a device or an entire factory.
Digital solutions
See tomorrow today. We support the digitization of your day-to-day operations by providing our solid industrial expertise and smart solutions to support your daily business needs.