Cleanrooms
A well-functioning production suite provides the basis for efficient production. We involve architects, engineers, operators and equipment suppliers to tailor cleanrooms according to your needs.
A cleanroom has multiple objectives. Primarily, it must protect the medicinal product from contamination and the operators from harmful substances. In addition, it must ensure an ergonomic work environment and accommodate the required equipment and utilities.
We have vast experience in cooperating with different cleanroom suppliers. Together we can define a cleanroom suitable for your operations.
Our cleanroom design starts by issuing a cleanroom User Requirements Specification (URS), which contains user requirements for design, operability, construction and validation. The key element is the cleanroom layout, as it provides the foundation for a functional and long-lasting production facility. In its design, we take into account logistics, process equipment, ventilation and many other details.
Cleanroom components
Our cleanrooms consist of cleanroom panels and a well-functioning ventilation system. We also help you create and monitor the required environment in the cleanrooms.
You have to consider many details to achieve the set requirements and targets for functional cleanrooms. We are here to help you.
To create and monitor the required environment in the cleanrooms, you need an automation system to operate the ventilation system and an independent environmental monitoring system to record the critical parameters in the cleanrooms. Many other aspects must also be taken into account. For example, the design and functionality of airlocks and pass-through boxes should be evaluated and tested by the operators to ensure they are fit for purpose.
To guarantee an efficient way of working, the access points for gases, clean water and other utilities must be placed in suitable locations. Doors with stoppers and ergonomic handles, multiple windows and sufficient lights create a better working environment for the operators. Door interlockings, access control and visible alarm lights guide the operators to react in a predetermined way.
Requirements and design
We design your cleanroom based on the User Requirement Specifications and the agreed layout. We also address the clear logistics of the cleanroom and containment of dangerous chemicals in the design.
The requirements and needs of your production process provide the starting point for designing your cleanroom. It is good to first align the layout together with all stakeholders.
When the first version of the layout is ready, we recommend conducting a review workshop involving architects, designers, operators and quality monitoring personnel. A well-designed layout that enables efficient personnel, material and waste flows is critical to successful production.
Based on the layout and process requirements, we issue the User Requirement Specifications for the cleanroom and its ventilation. We develop these based on your needs and the legislation, standards and guidelines issued. In this way we can demonstrate to the authorities that your production facility is compliant with its intended use.
By combining your knowledge about operations and product requirements with our extensive design experience, we can guarantee that the end result will meet your expectations.
Containment
According to experts, pharmaceuticals in the future will be more potent, and the need for containment of the production process will increase. Our experts can help you develop a suitable containment strategy.
Our priority is to minimize the open handling of the pharmaceuticals or intermediates in your production. To ensure containment and safety requirements, you often need to install RABS (Restricted Access Barrier Systems) or safety cabinets.
The second challenge is to install cleanrooms with sufficient filtering of the exhaust air and wastewater processing to ensure that pharmaceutical substances are contained within the cleanrooms. Personal protective equipment is also commonly needed.
The OEL (Occupational Exposure Level) and BSL (Bio Safety Level) are specified by the operators of the new facility. We then design the necessary containment methods accordingly. We also recommend conducting a thorough risk assessment of the production for operators and the environment before designing the layout of the cleanroom.
Modular design
The time to market is essential in new investment projects. Modular design and turnkey deliveries minimize the time at the site.
Designing and constructing cleanrooms in modules reduces the time needed at the site. Most of the construction can be performed in a cleanroom factory, which also minimizes waste and construction personnel at the site.
Our design considers the construction modules and adapts the concept for easy construction. The complete implementation is based on modules for the cleanrooms, process equipment and automation system. We can prioritize the procurement according to the delivery times of the critical components in the modules by utilizing our network of efficient and value-bringing suppliers.
We have also successfully delivered turnkey facilities for the pharmaceutical market for decades. These deliveries require even less involvement from your side. We deliver according to the user requirements and provide adequate training for your operators to take the new facility into operation.
Contact us
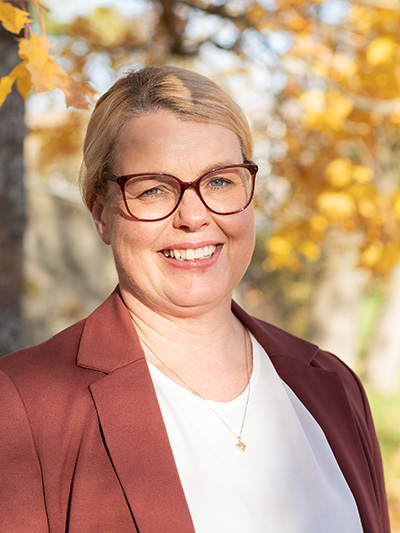
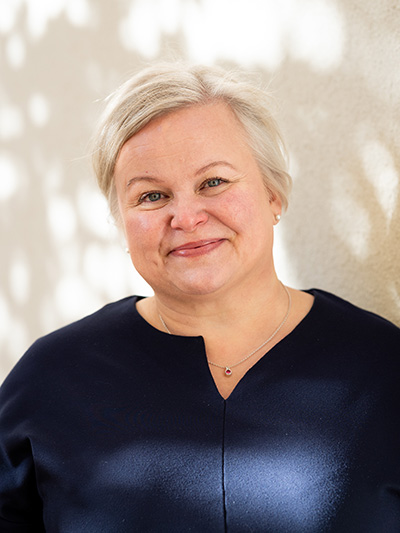