Hailia devised a way to upcycle surplus fish raw materials into delicious everyday food
Estimated reading time: 5 minutes
From idea to production in less than two years
The technology developed by Finnish startup Hailia offers an ecological alternative, for example, to tuna or minced meat. It enables the transformation of small pelagic fish or sidestreams from fish filleting, typically used as feed for livestock, into versatile food products. The company’s future plans include entry into international markets.
Hailia’s co-founders were working in the plant-based protein sector when they came up with the idea to build a business around herring. “Although being Finland’s most abundant catch, Baltic herring is underutilized as a food source, despite its excellent nutritional value and low carbon footprint,” says Hailia’s Managing Director, Michaela Lindström.
“Herring fishing benefits the Baltic Sea by reducing nutrient levels. Currently, over 80% of the fish consumed in Finland is imported,” she adds.
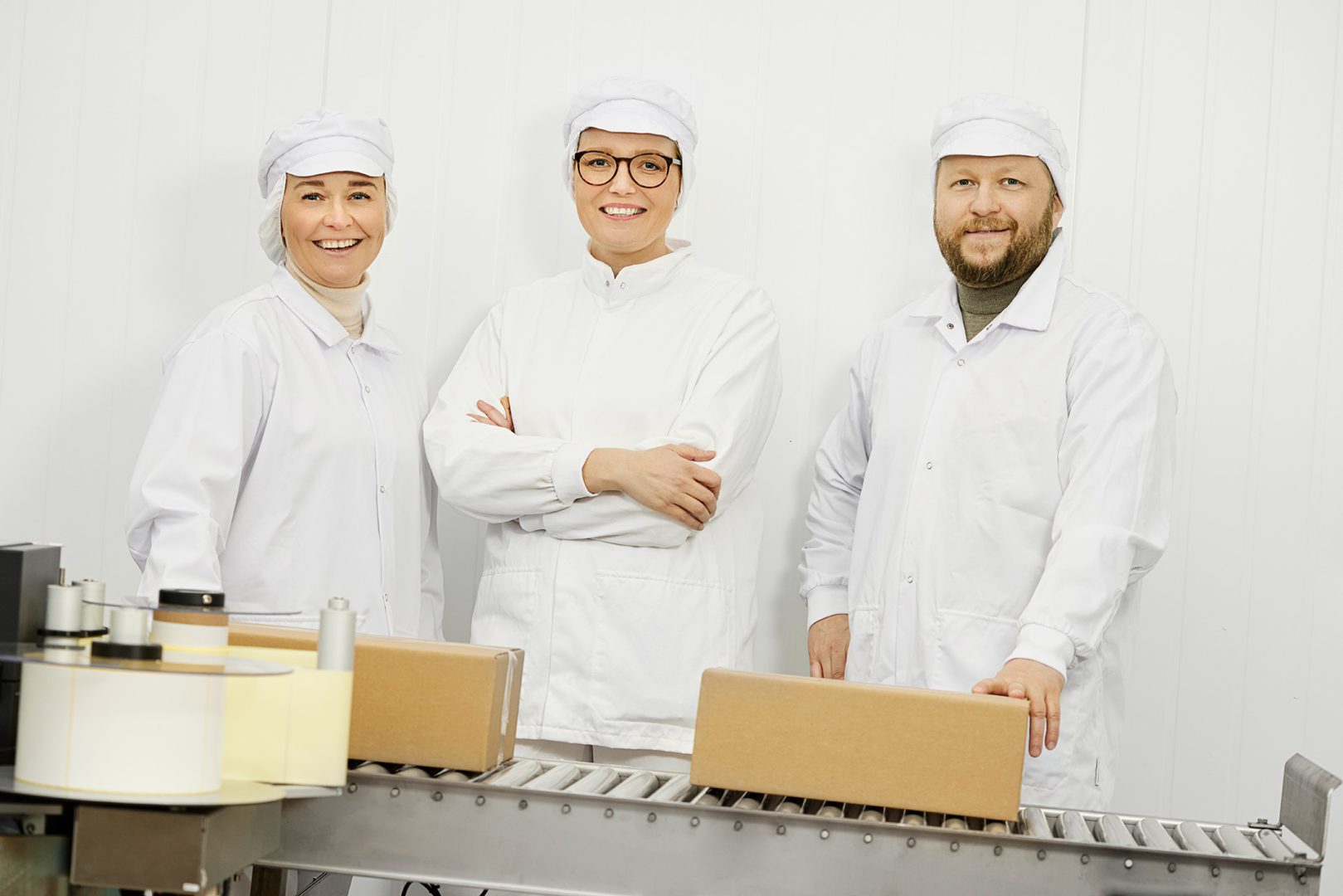
Hailia’s Managing Director Michaela Lindström, Production Director Taina Lahtinen, and Chief Technology Officer Otto Kaukonen.
Following the footsteps of plant-based protein sector
Hailia started building upon the research conducted at VTT Technical Research Centre of Finland.
“We were inspired by VTT’s pulled herring project and liked the idea that we need to package the raw material in a form that is easy, quick, and simple to use,” Lindström explains the concept.
Hailia decided to utilize all parts of herring under 15 cm in length that are usually used as feed, except for the heads and guts. One of the ingredients is oats. “The core of our product is the ability to create a texture similar to cooked fish fillet, without fishbones disrupting the mouthfeel,” Lindström reveals.
Currently, over 80% of the fish consumed in Finland is imported
Customer meetings from the outset
Once Hailia’s founders had secured investors and began advancing the project, they developed the idea and met with potential customers. “We aimed primarily at public sector kitchens. We wanted to offer them products that could replace red meat and imported fish like tuna,” Lindström specifies.
When the grants from the Centre for Economic Development, Transport and the Environment (ELY Centre) were secured, it was time to kick off the production planning process. Hailia chose Elomatic as their partner to assist in this undertaking, citing the company’s extensive expertise.
“Elomatic offered a wide range of services under one roof, from HVAC and electrical design to hygiene consulting. They were involved from preliminary planning to implementation and provided versatile assistance in documentation and bid preparation as well,” Lindström notes
Value of expert guidance during unexpected obstacles
Hailia’s intention was to acquire premises from the coastal town of Uusikaupunki. “We began outlining what changes were needed in the vacant factory property in Uusikaupunki and what the layout of the facility should be like. Additionally, we started surveying equipment suppliers and process options,” Elomatic’s Project Manager Taneli Arola explains.
As the work progressed and the electrical work was already underway, the property suddenly caught fire, leaving the entrepreneurs with no choice but to search for new premises. To their fortune, Elomatic stepped in to assist during this unforeseen situation. Eventually, they found a suitable old food factory in Karkkila.
“In the Karkkila property, we conducted surveys into aspects such as refrigeration systems and ventilation. Additionally, we acted as technical experts towards the property owner and arranged for a third-party condition assessment of the property before confirming that the premises were suitable,” recalls Arola.
Benefits of visualization
Arola tells that while Elomatic’s experts engaged in discussions with equipment suppliers, considered hygiene issues, and developed the process with Hailia, they also needed to capture the big picture on paper.
“When there is even a checkmark on the paper, it is easier to discuss. We had to understand how production works when building something entirely new – not just the physical systems, but also how people operate, how waste flows, and how to maintain an adequate level of hygiene,” explains Arola.
Elomatic also implemented mobile scanning in the empty premises. According to Arola, it was a cost-effective way to avoid unnecessary travel, as “there’s always one critical photo missing during site visits.”
Production currently operating at full capacity
Lindström reveals that scheduling challenges persisted even after the COVID-19 pandemic. Additionally, the later-retracted proposal by the EU Commission to ban herring fishing caused a slight delay in the launch. However, today the factory is in full production, and the company operates independently without Elomatic’s assistance.
“Many have wondered how, less than two years ago, we had an idea, and now we have a factory running and our product has been launched to the market,” Lindström tells.
Lindström cites smooth communication as one of the project’s success factors: “We were in contact weekly, sometimes daily, for a year and a half, and it felt like Elomatic’s experts were part of our team. We were also able to leverage their networks,” she describes.
“Working was easy because we were on the same wavelength the whole time and maintained a good atmosphere on both sides,” Arola agrees.
When there is even a checkmark on the paper, it is easier to discuss. We had to understand how production works when building something entirely new
Big plans
Lindström doesn’t shy away from the company’s ambitions: “We have big plans because we know there is demand for our technology and expertise. We know there are no similar companies worldwide.”
Arola states that the guiding principle throughout the project was minimizing waste: finding the middle ground that achieves crucial product safety in the food industry while considering investment costs and ensuring smooth operation in the factory’s daily routines.
Lindström emphasizes that just as Elomatic has been an extremely important partner for them, all of their employees have been important players throughout the journey: ” We have created a new fish product suitable for a variety of dishes, from soups to lasagna to pizza. We wouldn’t have achieved this alone.”
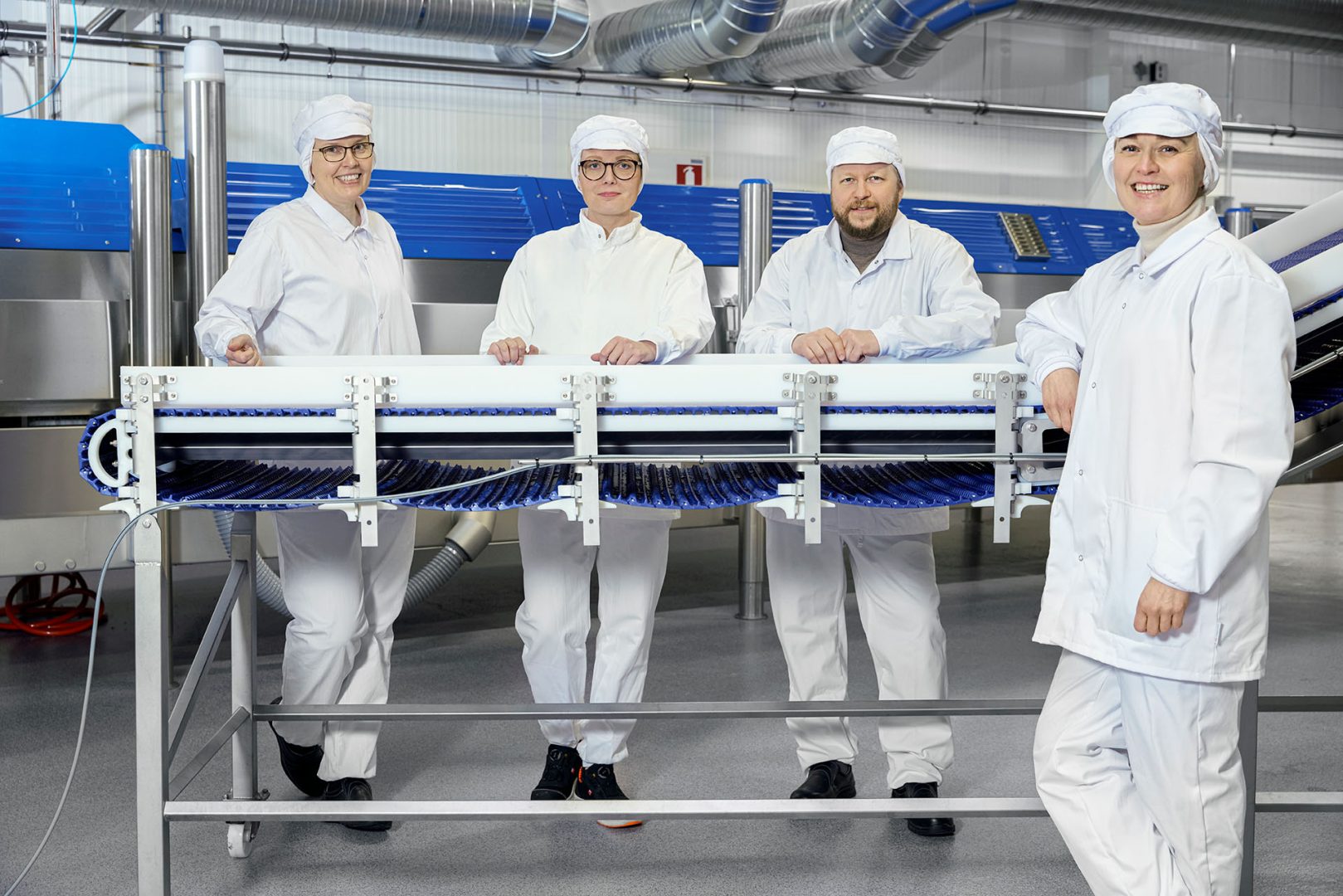
Michaela Lindström, Taina Lahtinen, Minna Kaunisto and Otto Kaukonen in Karkkila production facility.
Wanto to know more?
Process and Energy
We implement low-carbon and resource-efficient solutions across different industrial sectors. Are you looking for a partner for developing your production plants or promoting new investment? Our strengths include expertise in low-carbon energy solutions and a solid understanding of bio and circular economy projects.
Laser Scanning
We are a pioneer in laser scanning in Finland. We can measure in one day what would take a month when using the traditional methods.