Ensuring safety in ship design beyond existing rules: Leveraging the alternative design process
Author: Antti Yrjänäinen
Estimated reading time: 8 minutes
New solutions in ship projects must never compromise safety. However, some innovations, especially related to emerging fuels like ammonia and hydrogen, lack established regulations for ship applications. The alternative design and arrangements process is essential to ensuring safety in the absence of specific guidelines.
As ship machinery evolves with diverse fuel solutions, traditional “rulebook” methods struggle to define the safety levels of fuel storage and supply systems. Ship design is regulated by the SOLAS Convention, maintained by the IMO. Traditionally, its development has been reactive, shaped by lessons from past maritime accidents. While SOLAS provides comprehensive safety regulations, it does not directly address the challenges of new marine fuels.
Integrating new technologies requires case-by-case risk analysis, as prescriptive regulations may not apply. SOLAS’s alternative design and arrangements process provides a structured approach to incorporating unregulated technologies without compromising safety.
Alternative design process in brief
The core principle of the alternative design process is ensuring that safety levels meet or exceed those required by traditional solutions, demonstrated through thorough assessments and analyses. In practice, shipowners are required to apply for an exemption from the flag authority to deviate from standard SOLAS and classification society rules. The design must demonstrate, through calculations and risk scenarios, that it does not introduce greater risks than traditional solutions.
The process consists of two phases: the first focuses on identifying and analyzing potential risk scenarios, while the second quantitatively evaluates these risks and compares them to conventional safety standards. Effective risk assessment and mitigation are critical to achieving the required safety levels in both phases.
The core principle of the alternative design process is ensuring that safety levels meet or exceed those required by traditional solutions.
Driving low-emission fuel adoption
While alternative design is not a new concept, its importance has grown significantly due to the industry’s push for low-emission fuels. Ammonia and hydrogen, both carbon-free, are crucial for reducing shipping’s carbon footprint. However, they also introduce unique risks compared to traditional fuels. Despite these challenges, these fuels are being rapidly integrated into ship projects, often in the absence of established regulations.
While classification societies are working on developing rules, the IMO has yet to establish ammonia-specific guidelines, making alternative design crucial for safe implementation. Given ammonia’s toxicity, careful design and installation are vital to mitigate risks, particularly in the event of leaks.
Collaboration is key in preliminary analysis
The alternative design process begins by identifying risks associated with the target equipment or system. A diverse design team is formed, including stakeholders such as shipowners, equipment suppliers, designers, and representatives from ports and shipyards. Early involvement of classification societies and flag authorities is vital for smooth progress, with a skilled facilitator ensuring effective collaboration.
This phase usually occurs in workshops, where the alternative design’s goal is clarified, deviations from regulations explained, and alternative rules identified. The desired safety standard is also defined. Key outcomes include risk mapping, hazard assessment, identification of risk scenarios, and preliminary risk management strategies. These findings form the foundation for the next phase, where detailed calculations and analyses are conducted.
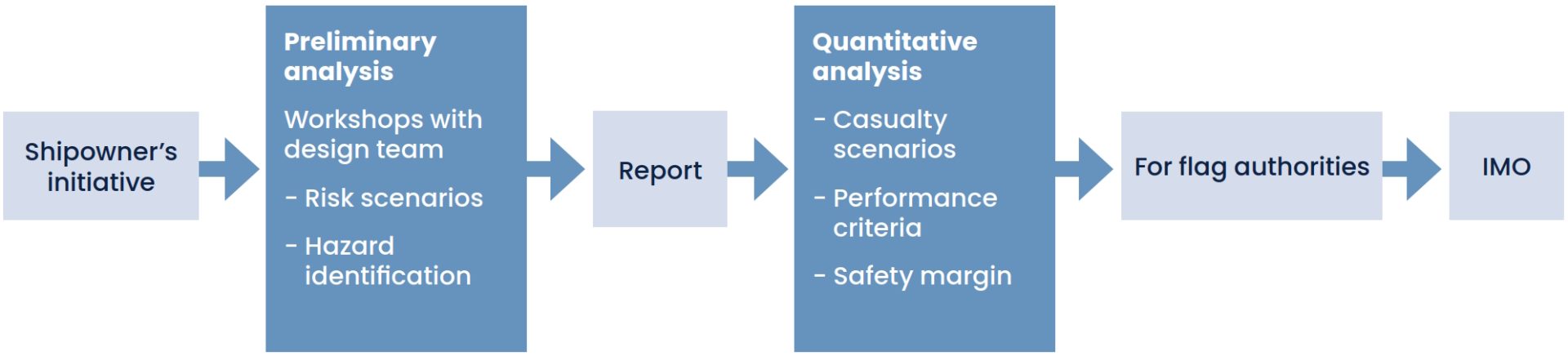
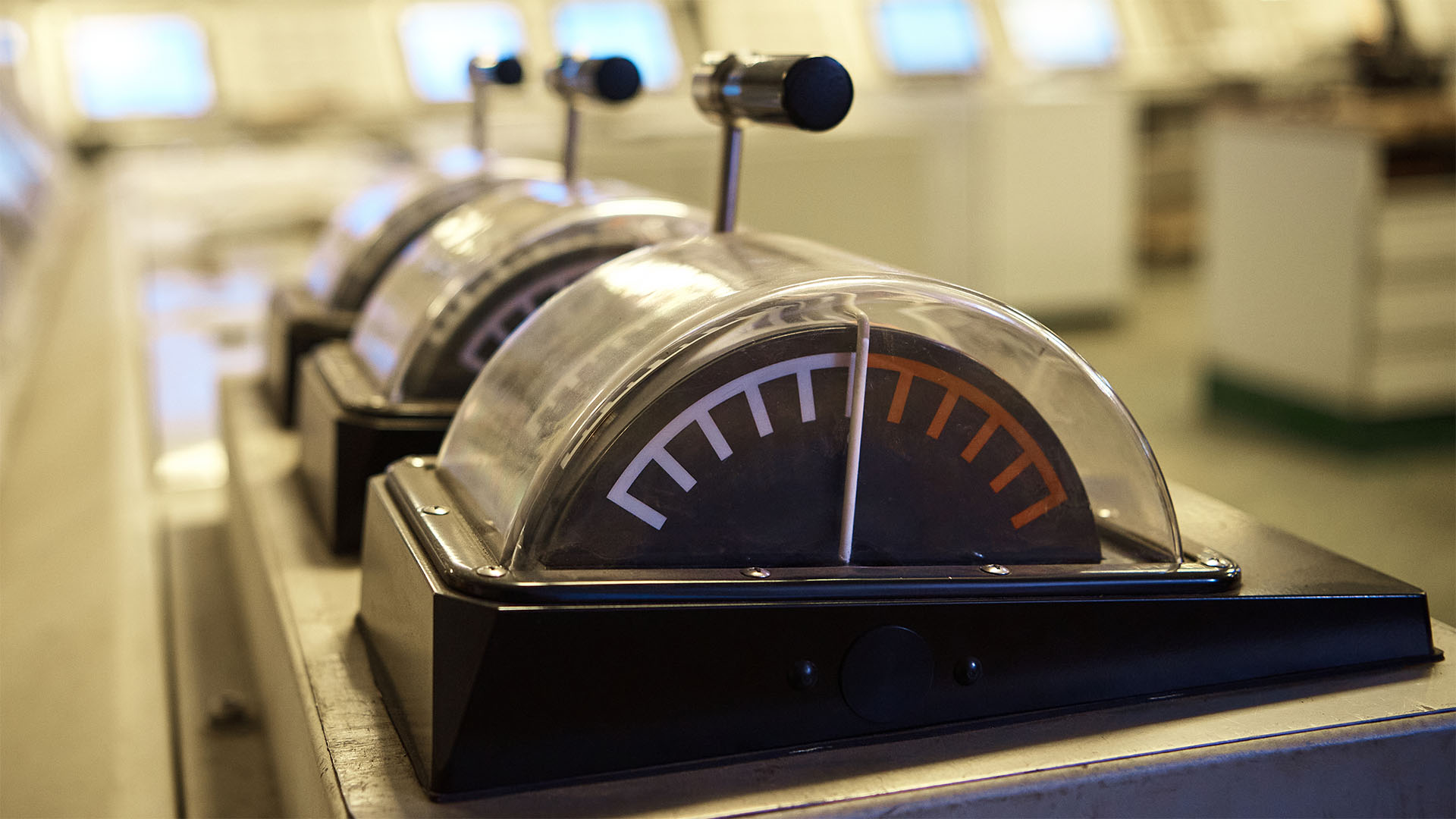
While alternative design is not a new concept, its importance has grown significantly due to the industry’s push for low-emission fuels.
Identifying risk scenarios and potential hazards
Risk assessment is a key element of the alternative design process, especially when integrating new technologies, and its findings must be incorporated into the actual design. It relies on established methods, two of which are presented here as complementary approaches. Rather than replacing each other, the first develops possible risk scenarios while the other focusses on identifying them.
The fishbone diagram, or Ishikawa diagram, is an effective cause-effect tool for uncovering root causes, especially in the early stages. It visually maps the relationships between various factors and their potential impact. The process starts by clearly defining the effect and then developing scenarios that could lead to that. These scenarios are categorized using a framework like 6xM*, enabling structured analysis and a more focused approach to identifying solutions.
*6xM stands for Manpower, Machine, Mother Nature, Materials, Measurements, and Management.
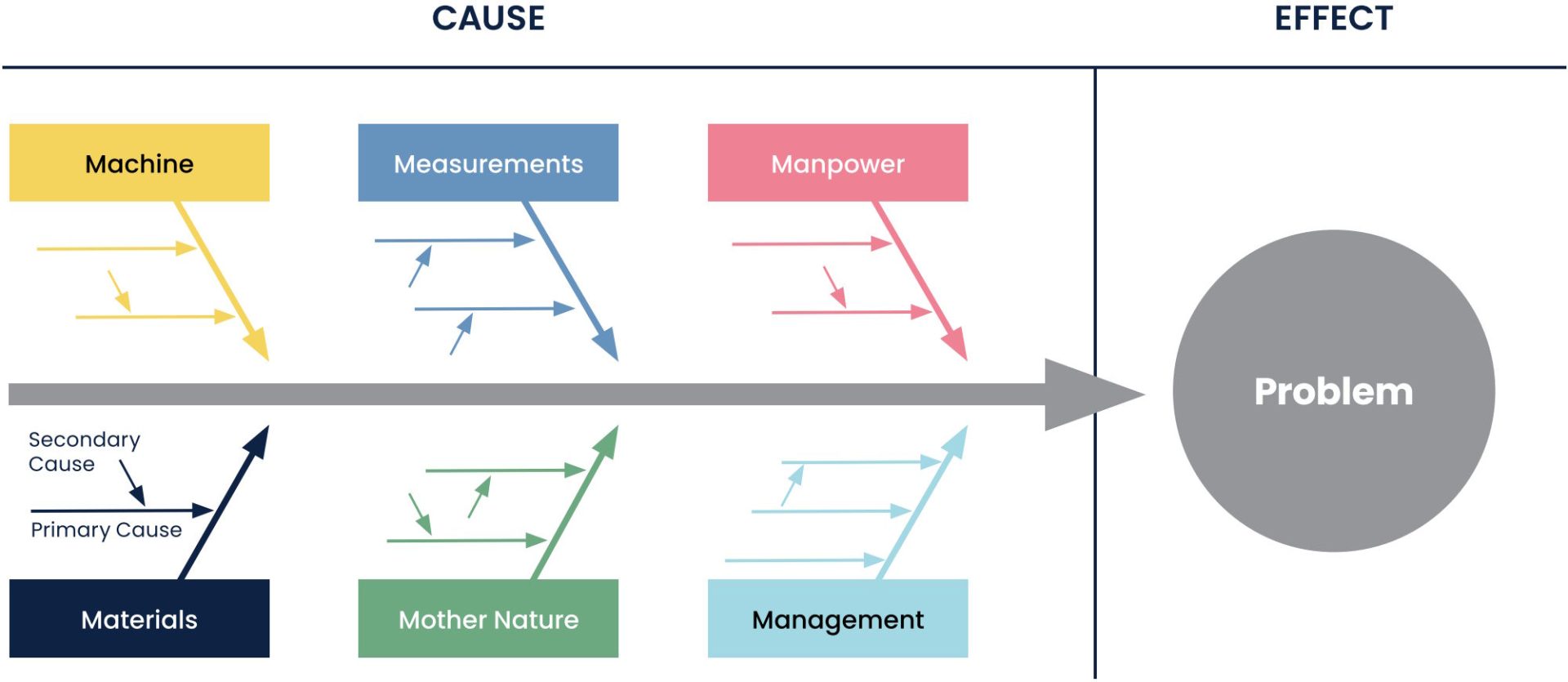
HAZID (Hazard Identification) is a widely recognized risk assessment method that focuses on identifying potential risks. It provides a qualitative evaluation through visual mapping. For a thorough evaluation, it is essential to involve a carefully selected design team, including experts with different perspectives. The findings from the HAZID study are integrated into the design process, covering aspects like equipment, piping, fire protection, and instrumentation.
HAZID in practice
HAZID sessions are conducted in two stages: the first focuses on identifying risks, while the second evaluates their significance and frequency. A one-to-two week break between stages is recommended to allow time for refining the observations. Risk reduction strategies can be technical, procedural, or operational, depending on the scenario.
The first step involves dividing the system – such as pipes and equipment – into logical components, while categorizing ship operations into phases like bunkering, cargo handling, maneuvering, and operation. A thorough risk assessment must consider all factors, including design and installation, operation, and administrative risks.
After risks are identified, their severity and likelihood are evaluated, and a risk matrix is created to prioritize significant risks. The risk level is determined by assessing both the probability and impact of each identified hazard. If a risk exceeds the acceptable threshold, measures are implemented to reduce its probability or frequency. For example, a fire-hazardous leak might be mitigated through inerting to prevent fire hazards.
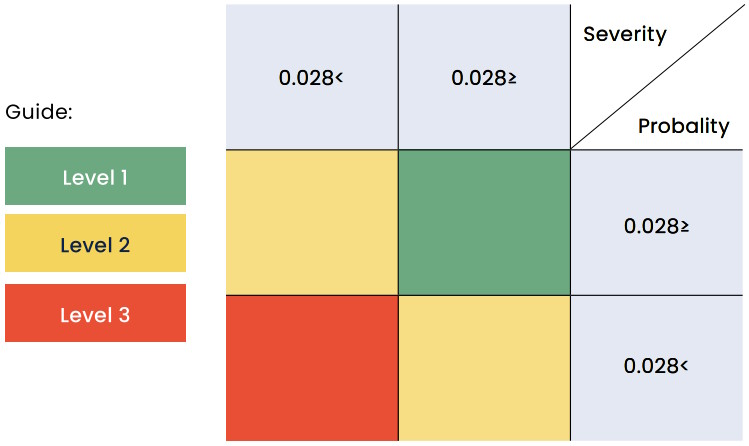
Quantitative analyses for final design approval
Complex alternative designs often require quantitative analysis, including physical testing. These assessments evaluate risks over time, considering design, operational, and regulatory factors – especially when working with new fuels like ammonia. In addition to identifying risk scenarios, the required performance criteria and corresponding safety margin are defined, accounting for potential methodological uncertainties. The performance level is then assessed against criteria for human safety, equipment integrity, and environmental impact.
For ammonia applications, its toxicity must be carefully addressed, making quantitative analysis essential for assessing leak dispersion. Since ammonia reacts with moisture in the air, leaks can spread with rain, potentially increasing risks in surrounding areas. Computational Fluid Dynamics (CFD) simulations help model the spread of toxic emissions. In addition to equipment and systems, risk management tools such as Failure Mode and Effects Analysis (FMEA) for a structured approach to discovering potential failures.
A comprehensive final report consolidates both qualitative and quantitative findings, demonstrating compliance with safety requirements. This report serves as the foundation for evaluation and approval by administration (flag authority), who submits that information to IMO.
Future of alternative design in marine fuel solutions
As ship machinery systems evolve with diverse fuel options, traditional regulations are increasingly challenged in addressing their impact on fuel storage and safety. As a result, alternative design methods will play a growing role in future projects, before the final rules are established. Their successful implementation requires a thorough understanding of the process and its careful application. In this writing, alternative fuels have been the focus. However, the alternative design approach and the presented methodology are valid for any other case where the design goes beyond existing rules.
Effective risk assessment is essential and requires a multidisciplinary team of experts. With skilled facilitation, this team can conduct targeted analyses, ensuring both efficiency and reliability. This approach supports the safe integration of new fuel solutions aboard ships, minimizing risks while optimizing operational performance.
The “Five Whys” method: A practical approach to root cause analysis
A functional method to identify the root cause of a defined problem is the “Five Whys” technique. This approach involves asking “why” multiple times until the root cause is uncovered. Brainstorming sessions are an effective way to move forward in this process. For example, consider a hypothetical problem of a ship running aground.
The investigation might proceed as follows:
- Why did the ship run aground? – Because the steering didn’t work.
- Why didn’t the steering work? – Because the rudder didn’t respond to the helmsman’s commands.
- Why didn’t the helmsman’s commands reach the rudder? – Because the circuit board of the steering system was damaged.
When no further questions can be answered, the root cause can be identified, which, in this case, is the damaged circuit board causing the grounding.
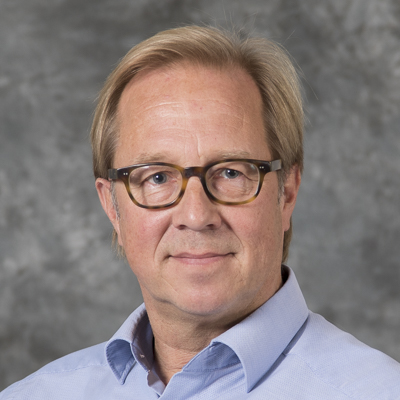
Antti Yrjänäinen
M.Sc. (Naval Arch.)
Antti is a Project Manager responsible for the Shipowners and Operators customer segment. Before his current role, he worked on early-stage ship design, ship concepts involving alternative fuels, lifecycle-related projects, and marine consultancy.
antti.yrjanainen@elomatic.com
Sources
- IMO MSC1./circ 1212 /Rev. 2 26 June 2024; Revised Guidelines on Alternative Design and Arrangements for SOLAS Chapters II-1 and III
- IMO MSC1./circ 1455 Guidelines for Approval of Alternatives and Equivalents as Provided for in Various IMO Instruments
Want to know more?
Reducing MS Crown Seaways’ fuel consumption with Elogrid: An installation story
DFDS A/S has installed Elogrid™ on the MS Crown Seaways to enhance the ship’s energy efficiency and reduce carbon emissions. The installation was successfully completed during the vessel’s annual drydocking at the Fayard repair yard in January 2024.
Design and Engineering for a Canadian Polar Icebreaker
Elomatic is reaching the next phase in the design of a Canadian Polar Icebreaker ship which is set to be built by 2030. The Canadian Polar Icebreaker project was originally initiated in 2012 by the Canadian Government as a replacement for the CCGS Louis S. St-Laurent, Canada’s current largest icebreaker. However, it was put on hold for almost 10 years before being reignited in early 2021.